Find Our Products
Silicone Products
At Melon Rubber, we specialize in high-performance silicone solutions for medical, automotive, and consumer industries. With expertise in LSR injection molding, FDA-certified silicone parts, and fast prototyping, we deliver custom silicone seals, gaskets, and components that meet the highest quality standards. Whether you need small-batch prototypes or mass production, our ISO-certified facility ensures precision, durability, and competitive pricing.
Why Choose Melon Rubber?
✅ FDA & ISO-Certified Production
✅ Fast Turnaround: Prototypes in 7 Days
✅Low MOQ (from 500 pieces)
✅Part Tolerance meets ±0.01mm ( ISO3302-1M2/RMA)
✅ Custom Solutions: From Design to Delivery
✅ Global Export Experience,Seamless logistics support for EU, North America, and APAC markets. FOB/CIF terms available.
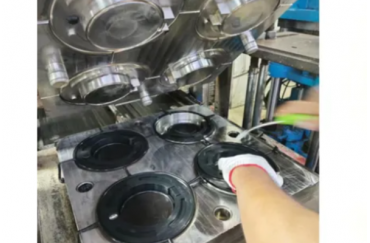
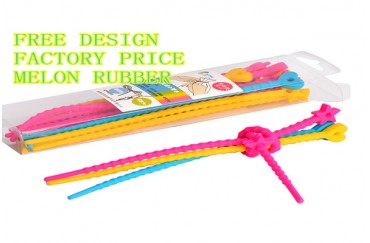
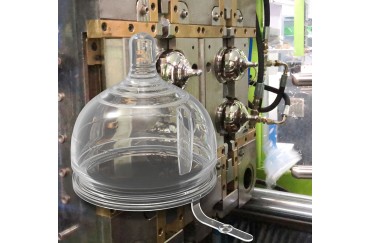
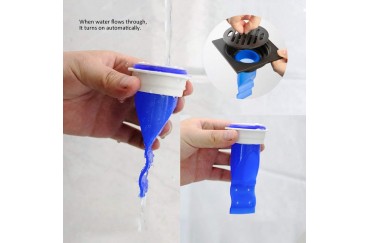
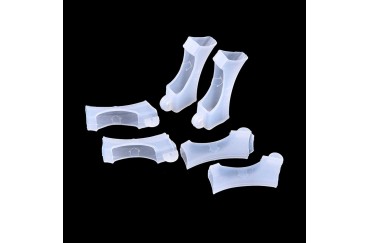
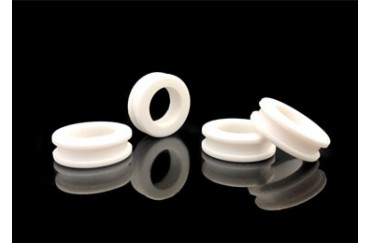
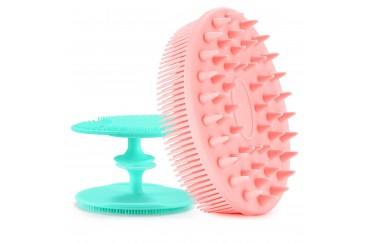
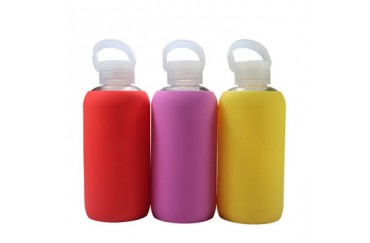
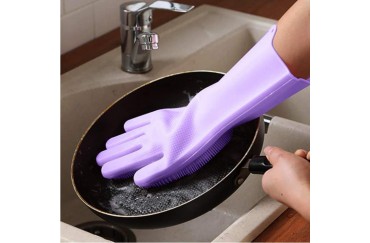
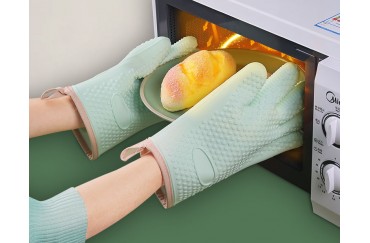
Custom Silicone Products Manufacturer | Precision Solutions for Global Industries-Melon Rubber
At Melon Rubber, we deliver:
✅ 7-15 Day Lead Times – Meet urgent deadlines without compromising quality.
✅ Full In-House Capabilities– From prototypes to mass production, we handle compression, injection, and LSR molding under one roof for faster turnaround.
✅ Material Expertise – Silicone hardness from 20 to 80 Durometer, with options for medical-grade, oil-resistant, FDA-approved, USP Class VI, ISO 10993 biocompatible, and fire-resistant materials.
✅ Custom Solutions– Precision-engineered seals, gaskets, O-rings, grommets, dampers, diaphragms, wire seals, overmolding, and complex geometries.
✅ Competitive Pricing – Optimized for both small-batch prototypes and high-volume production.
▶︎✅Advanced Silicone Manufacturing Technologies
LSR injection molding
Ideal for complex, high-precision parts with tight tolerances (±0.01mm)/for baby silicone products
▶︎ Medical-grade liquid silicone rubber (Wacker LSR3003 series)
▶︎ Multi-cavity molds for high-volume production
▶︎ Cleanroom manufacturing (Class 100,000)
▶︎ Automated process for high yield and consistency
▶︎ Ideal for medical and baby-safe silicone products
▶︎ Short curing time: 30 seconds to 2 minutes
Learn More About LSR
Compression-molding
Cost-effective solution for seals, gaskets, and industrial components
✅ FDA & ISO-Certified Production
✅ Fast Turnaround: Prototypes in 7 Days
✅Low MOQ (from 500 pieces)
✅Part Tolerance meets ±0.01mm ( ISO3302-1M2/RMA)
✅ Custom Solutions: From Design to Delivery
✅ Global Export Experience,Seamless logistics support for EU, North America, and APAC markets. FOB/CIF terms available.
Extrusion Molding
Perfect for silicone tubes, seals, and strips with consistent cross-sections
▶︎ Low-cost materials and tooling
▶︎ High-volume production with short lead times
▶︎ Wide applications: medical tubing, wire insulation, and more
Explore Extrusion Molding
Ready to Start Your Silicone Project?
Upload your 3D files or discuss your requirements with our engineers.
Fast turnaround for prototypes and short-run production